The production of furniture or other wooden objects involves, on the one hand, making the object itself and, on the other hand, finishing it. I have often observed that a lot of energy and resources are expended in order to achieve the first part as close to perfection as possible, but unfortunately, the finishing part is almost neglected. I say unfortunately because the finish is where the eye falls first and a botched finish negates all the effort put into the woodwork. The quality of the finish is as much about the quality of the finishing products as it is about the correct choice of spray gun.
The application gun is part of an application system. This system can be chosen in such a way as to increase the quality of the finish, but also to improve the efficiency of the whole process. A good choice of spray system:
- reduce the cost of finishing materials
- increase productivity
- reduce pollution
- reduce material losses
- meets environmental protection requirements.
Several basic systems are used to finish wood, each with its advantages and disadvantages. Let's take them one at a time.
CONVENTIONAL spraying is the most flexible and adaptable method of coating wood. It consists of spraying the material through the nozzle of a gun with compressed air at a pressure of 3-5 bar. When the reservoir is above, the material used free-falls out of the gun by gravity, and when it is below the nozzle the material is absorbed from the pressurized reservoir. The amount of material is regulated by the supply of compressed air.
Advantages: uniform coverage, possibility to use different materials, good quality, simple method of adjusting jet width and material consumption.
Disadvantages: low productivity, high solvent consumption (low viscosity materials must be used), considerable material loss during spraying (65-75%).
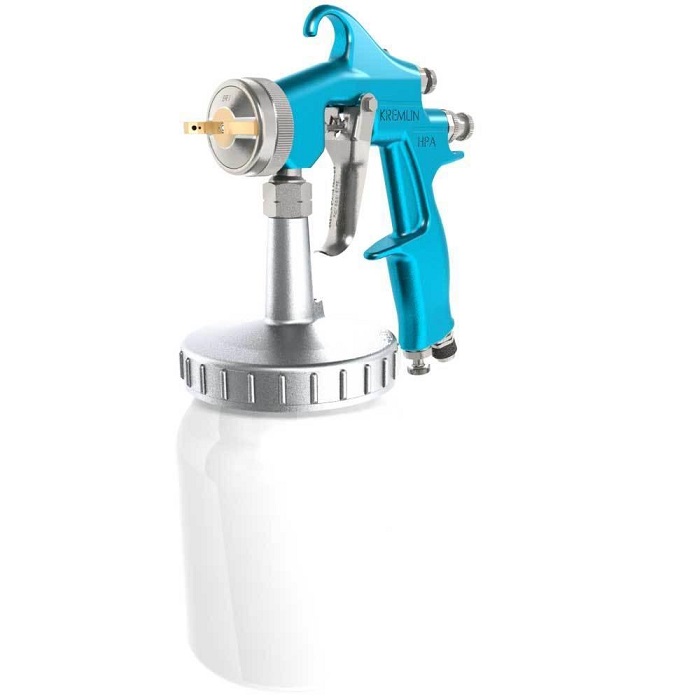
High Volume Low Pressure or HVLP (High Volume Low Pressure) spraying has a modification compared to conventional spraying in that the compressed air pressure coming out of the gun is no more than 0.7 bar. The modification was made in order to reduce high material losses.
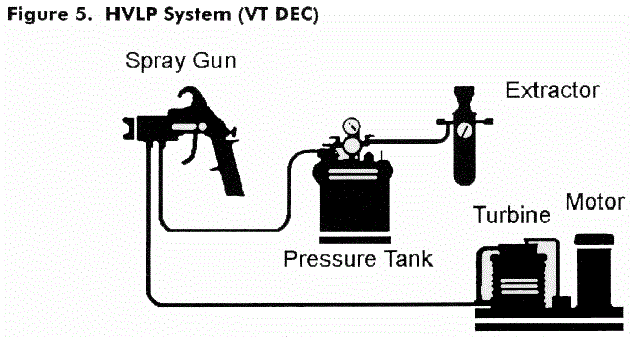
Advantages: uniform coverage at low pressure, good quality, easy adjustment of nozzle and material consumption, material saving compared to conventional spraying.
Disadvantages: low productivity, high solvent consumption (use only with low viscosity products).
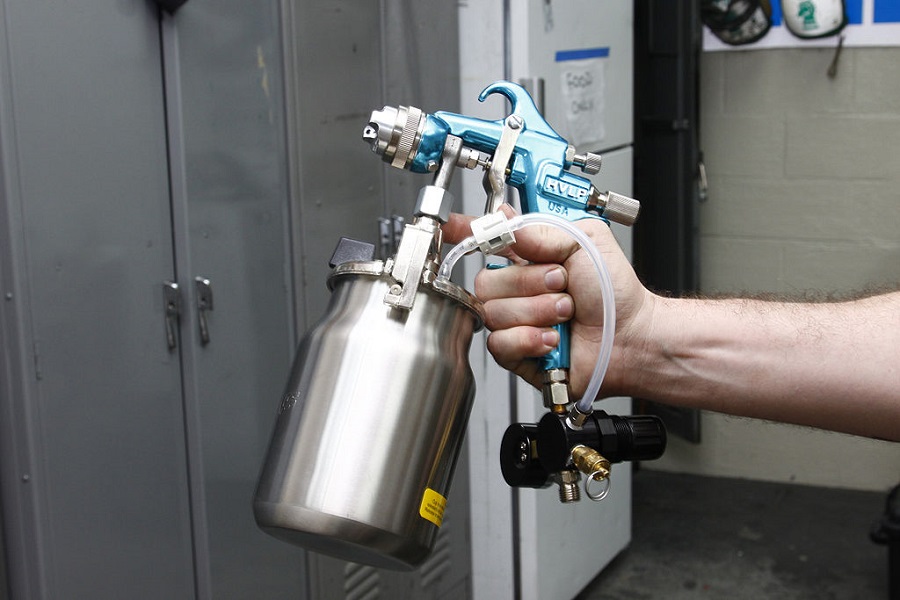
AIRLESS or high-pressure spraying is achieved by means of a high-pressure pump that presses the material without compressed air (the material is not mixed with air) through the nozzle with a pressure of 90-360 bar. The jet width can only be adjusted by changing the nozzle of the gun.
Advantages: high productivity, possibility to use high viscosity coating materials, reduced material losses, material transfer efficiency
Disadvantages: difficult jet adjustment (by changing the nozzle), low coating quality compared to HVLP
AIRMIX® spraying is a combination of low-pressure and high-pressure spraying. The material is passed through the nozzle at a lower pressure than in the airless method (20-120 bar). The compressed air pressure used to adjust the jet is no more than 1.5 bar. The method is a compromise combining the advantages of low-pressure and high-pressure spraying and is the most widely used method to obtain a very good quality coating.
It is one of the medium-pressure methods, just like the AAA (Air-Assisted Airless) system, but it works much better. AIRMIX is a registered trademark of Sames Kremlin, created by the Kremlin in 1975. The concept was a tremendous success, turning a common technology into a worldwide industry standard. Over time, Kremlin has also developed the second generation of Airmix guns - Gun Aircap Adaptation - which achieves jet adjustment without changing the nozzle, saving time and money. Guns and spray systems Sames Kremlin are distributed in Romania by Falk Consulting.
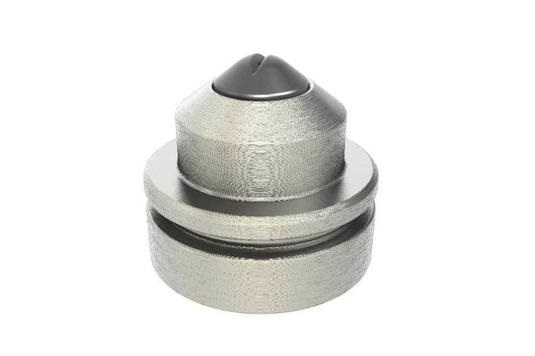
Another application system - described in a separate article - is electrostatic field spraying.
In conclusionEach system has its advantages and disadvantages, and the choice should be made in such a way as to maximize the benefits. Important to remember is that:
- Conventional spraying is chosen when productivity is not a priority, consumption is low, materials used have low viscosity.
- HVLP is a good choice for small workshops that want a reduction in material waste, do not need high productivity, and the applied materials have low viscosity.
- Airless systems are used when productivity is a priority and when applying viscous materials. It is a good choice for applications that protect and less so for high quality applications.
- Airmix offers good material transfer efficiency while resulting in very good surface quality. It is one of the best choices, but not recommended where paints contain larger particle sizes, where productivity is not a requirement or the volume of work is low, nor when painting hard to reach areas.
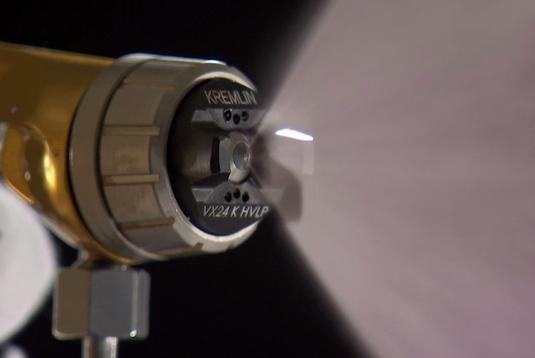
Add comment