With their flowing shapes, boats have always charmed. A boat is a wellspring of beauty, but if it's built by your own hand, and especially if it's made of wood, things could get out of control and into the realms of addiction and ecstasy. For those who are willing to take the risk, here's how to build a boat from A to Z. Since for most Romanians the waters are far away, I chose a lightweight construction, under 20 kilograms, a canoe that can be easily transported on the bars of the car to the nearest river or lake. A boat is a demanding and special thing, which is why you should not be surprised if the cost of materials will run around 1,000 lei.
There are several methods of building light boats but because of its simplicity I have settled on the one known as "stitch&glue". This method can be tackled even by a first-time builder and is basically similar to tailoring. The material required is plywood, from which the component parts are cut out, sewn together with brine, glued along the seams and stiffened with fiberglass.
The first step is to find a project. There are websites offering various plans at affordable prices or even for free, but for beginners I recommend Michael Storer's simple designs (https://www.storerboatplans.com/design/boatplans/). The canoe I am presenting is the Kymi River 16 (https://www.woodenboat.com/boat-plans-kits/kymi-river-16), a more elaborate construction that I chose for its beautiful shape.
Once we have the project we will need to source our materials. For Kymi River we need two sheets of 4mm thick plywood, 1220/2500cm in area, and if we are talking about boats we are automatically talking about nautical plywood. The nautical plywood has the quality of not peeling under the action of water or humidity, both because of the wood essence (okoume) and because of the glue with which the veneer sheets have been glued together. In Romania, okoume plywood can be purchased from Holver at a price of around 120lei per pound. We also need fiberglass and epoxy resins (epoxy, not polyester!) with which to impregnate the fiberglass fabric. Fiberglass is sold as cloth, one meter wide. It is woven in different thicknesses, and its specific weight is used to differentiate it. For canoes we need fiberglass of 160 grams/square meter or, if we can't find it, a maximum of 200, 15 linear meters.
The epoxy resin is a two-component chemical compound (the resin itself and the "hardener"). The preparation of the resin for impregnation is done shortly before use by mixing the two components in the proportion specified in the product data sheet (EPIPHEN RE 4020 + CATHALYST DE 4020), for a light boat about 5 liters are needed. Both the fiberglass fabric and the epoxy resin can be purchased from Polydis. A linear meter of fiberglass costs about 10 lei and a kit of 5 liters of resin + hardener costs about 600 lei. We also need 15 meters of copper wire with a cross-section of 1.5 square millimetres (available from the electrical store as Fy 1.5 insulated conductor, which can be stripped at home with a cutter), sandpaper of various grain sizes and a few wooden slats to be bought on the way.
With these materials we can take care of the tools. For cutting the plywood we need an electric pendulum saw, and for the rest we need the usual tools: a router, handsaw, handsaw, patent, drill, etc. We also need a covered area of 6x3m, protected from the elements. Because epoxy resin only polymerizes at temperatures above 20C, if we want to build in the cold season we need to have access to a heated workshop (garage), whereas if we build in the summer months a shed is sufficient.
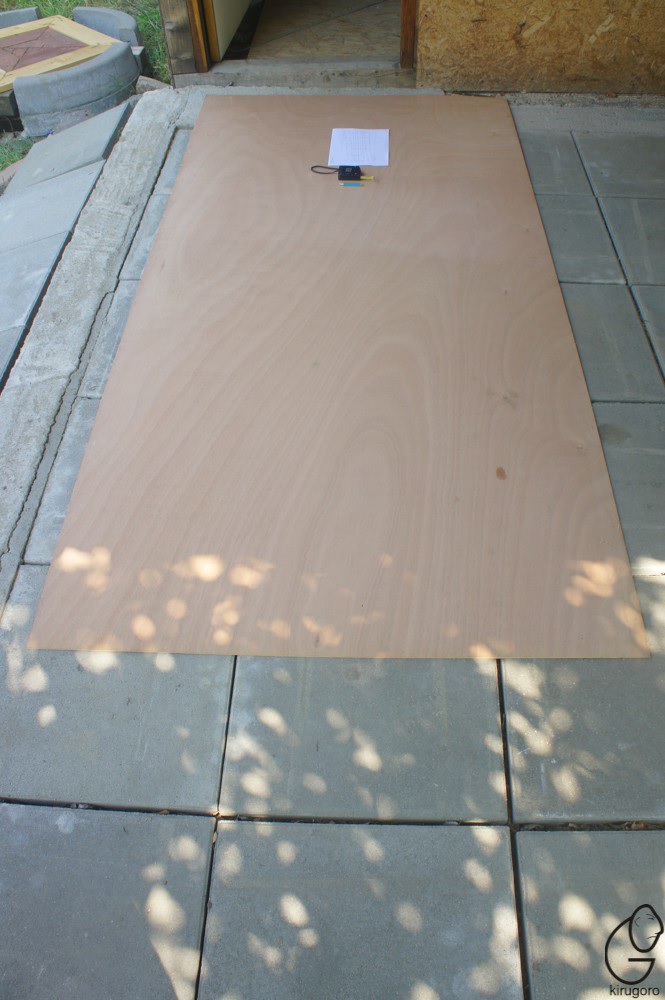
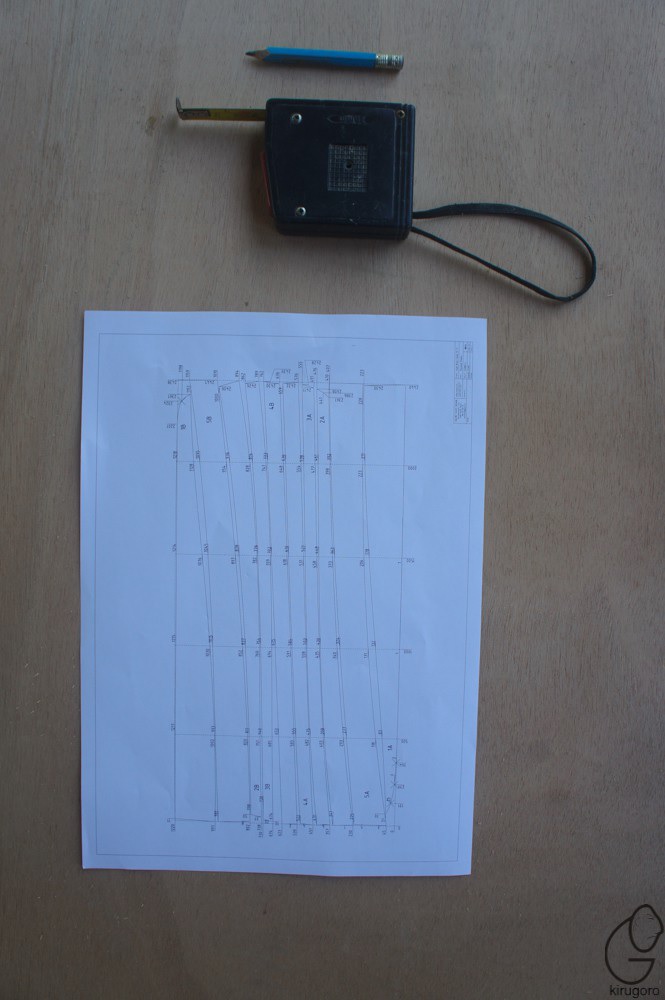
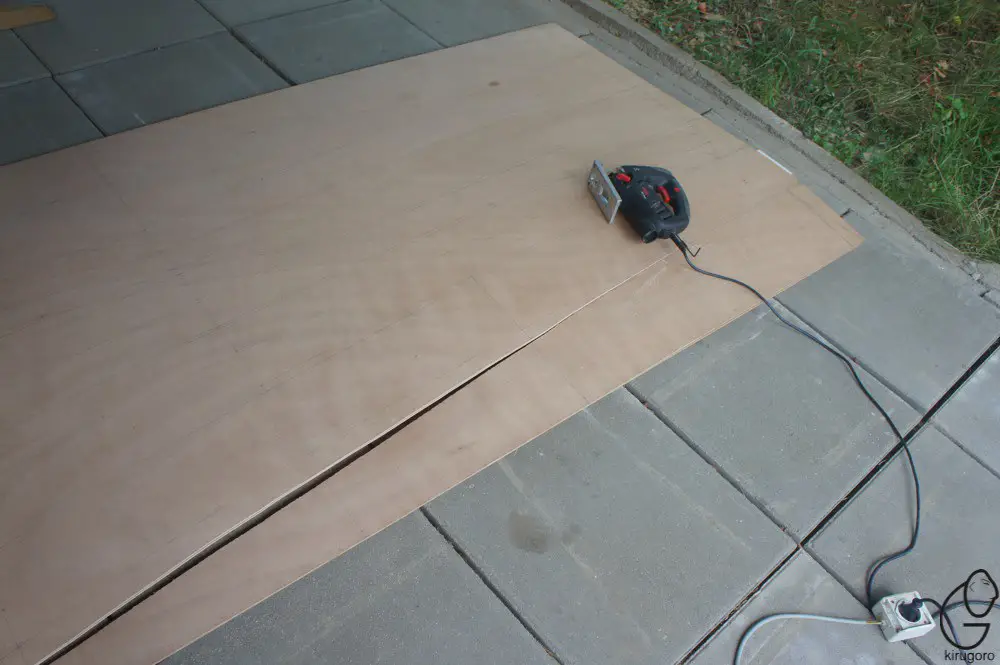
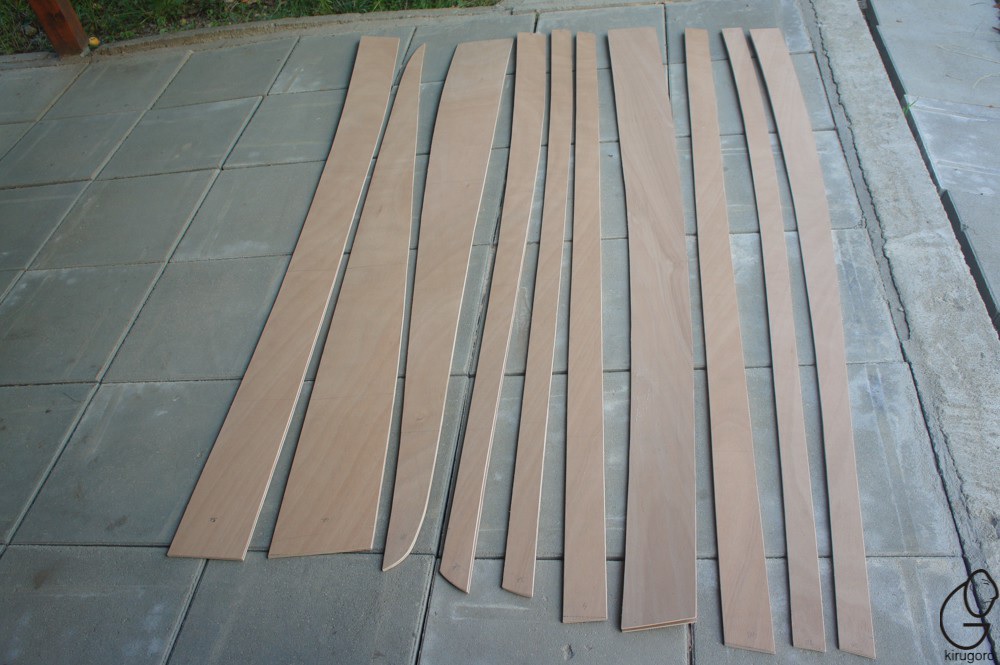
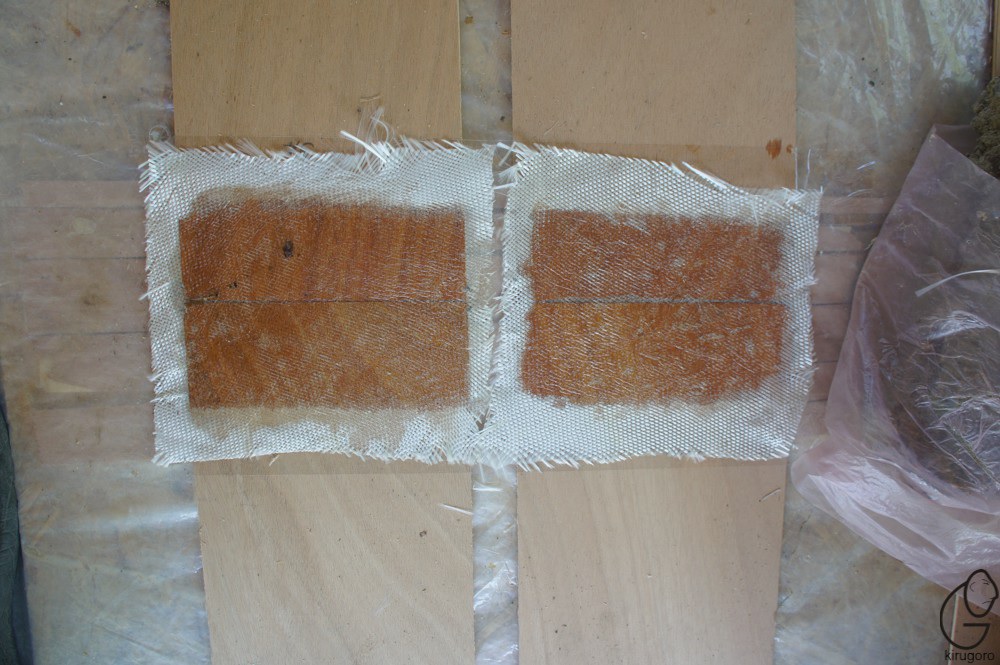
The first operation consists in tracing the boat's elements on the plywood. There are several ways to do this, but the Kymi River 16 plans are described by a set of X-Y coordinates spelled out in a plan. Transposing these points onto the plywood by ruler measurements will give a set of points which we then join with straight lines. Since the boat is symmetrical, it is not necessary to draw the landmarks for the left and right sides of the boat, but we will draw a single plywood sheet which we will superimpose and glue to the second one with double-stick tape and cut the sheets at the same time.
At the end of the cutting operation we will obtain curved strips called fillets. Since the canoe is 5m long and the plywood is only 2.5m long, two fillets will have to be glued end to end, one in extension of the other. The operation is done with epoxy resin and for strength, the gluing is "reinforced" with fiberglass strips, front/side.
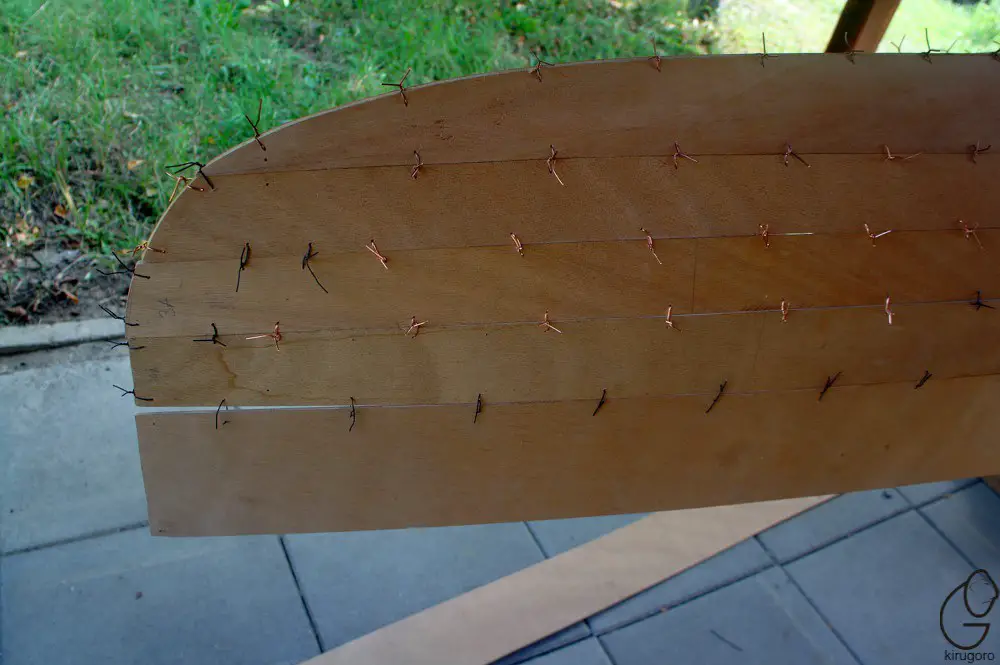
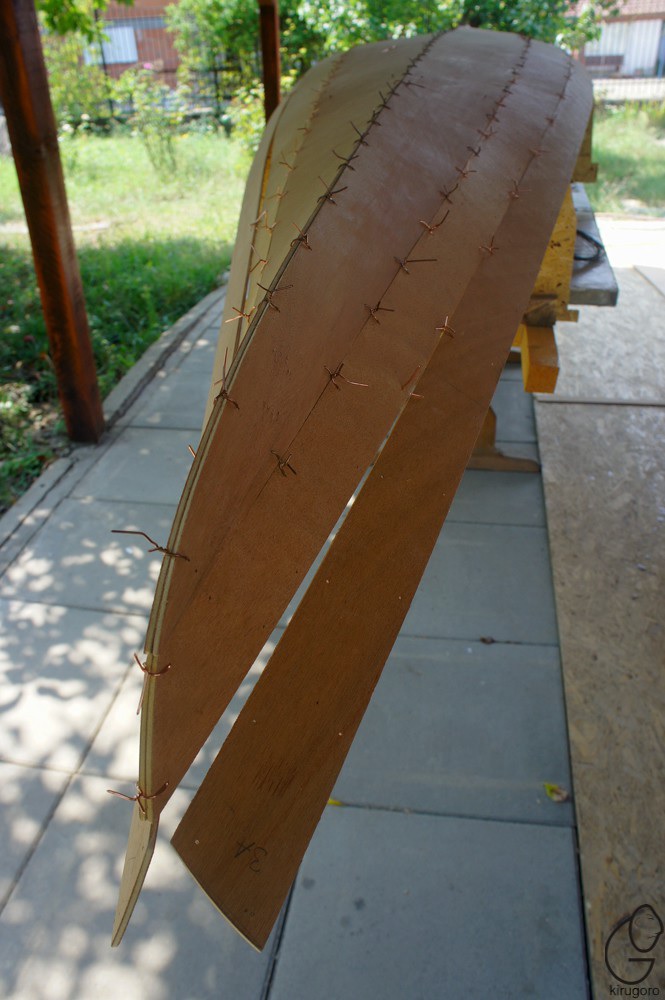
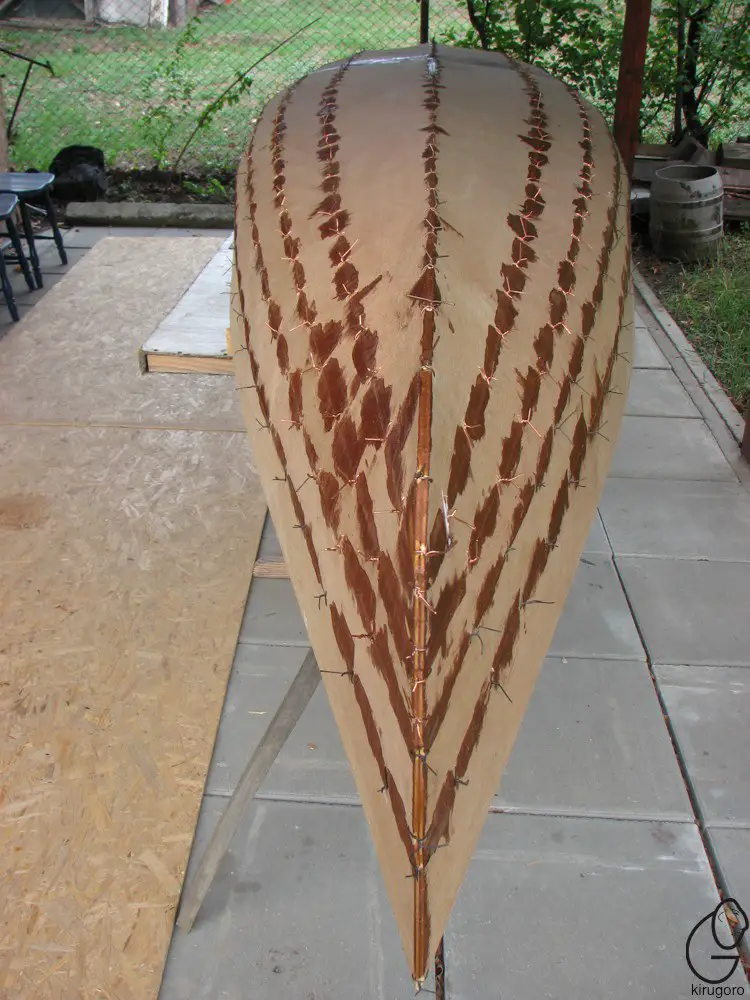
To proceed to the 3D shape of the boat we need to sew the perimeter of the plywood fillets with copper wire. The preparation for this is done by making equidistant holes (every 15 cm) in the contour of the fillets, which are sewn in pairs, two by two with copper wire loops twisted together. At the end of this work, we will be able to see the boat for the first time in its full size and imagine ourselves walking around in it, which will sustain our enthusiasm and keep us going. The ropes are a temporary accessory that we will dispense with once we have glued all the fillets to the contour with strings of epoxy resin thickened with wood flour (fine sawdust).
Once we get rid of the wires, we can say that we already have the boat, it just needs to be strengthened by adding a layer of fiberglass, called 'laminating'.
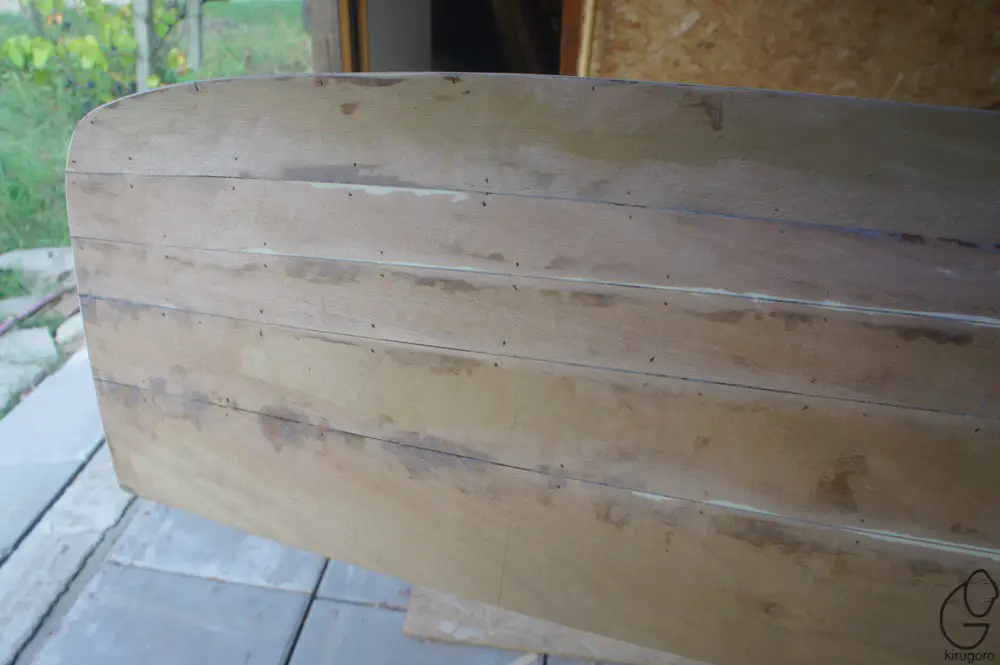
Lay the fiberglass fabric over the plywood body and "drape" it dry with a brush until it is perfectly seated without wrinkles, then pour the resin hardener mix over it and spread evenly over the entire surface with a squeegee, brush or trafalquet. Since the resin becomes viscous within a few minutes of mixing, prepare successive doses, small enough to allow time to spread them before hardening. When the entire surface of the canoe is covered with resin, wait about 10 hours and apply the next coat, repeating
3-5 times (or as many times as needed until the fabric is completely covered).
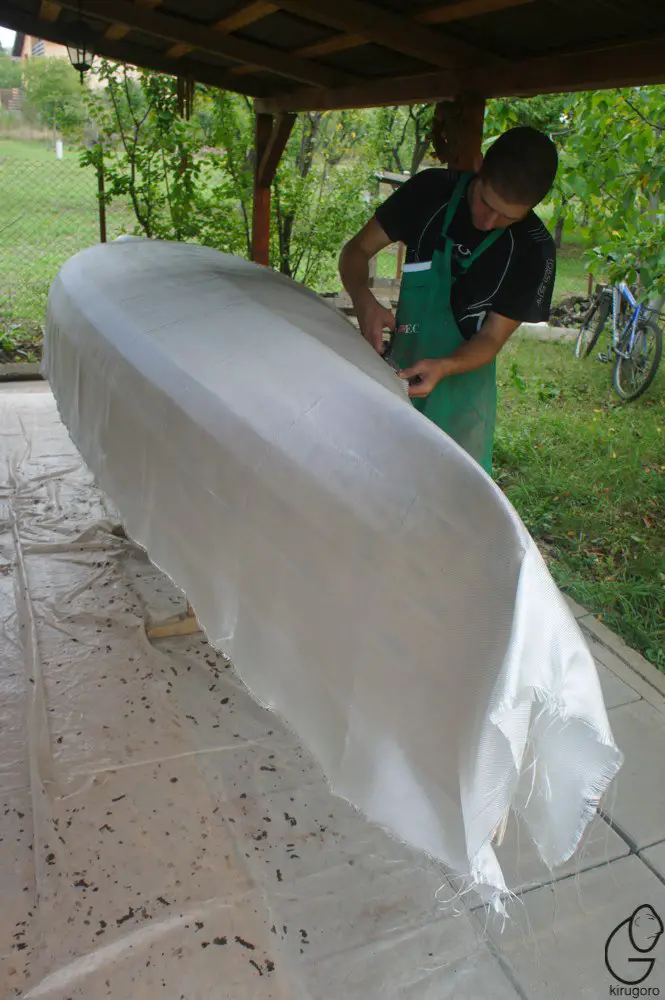
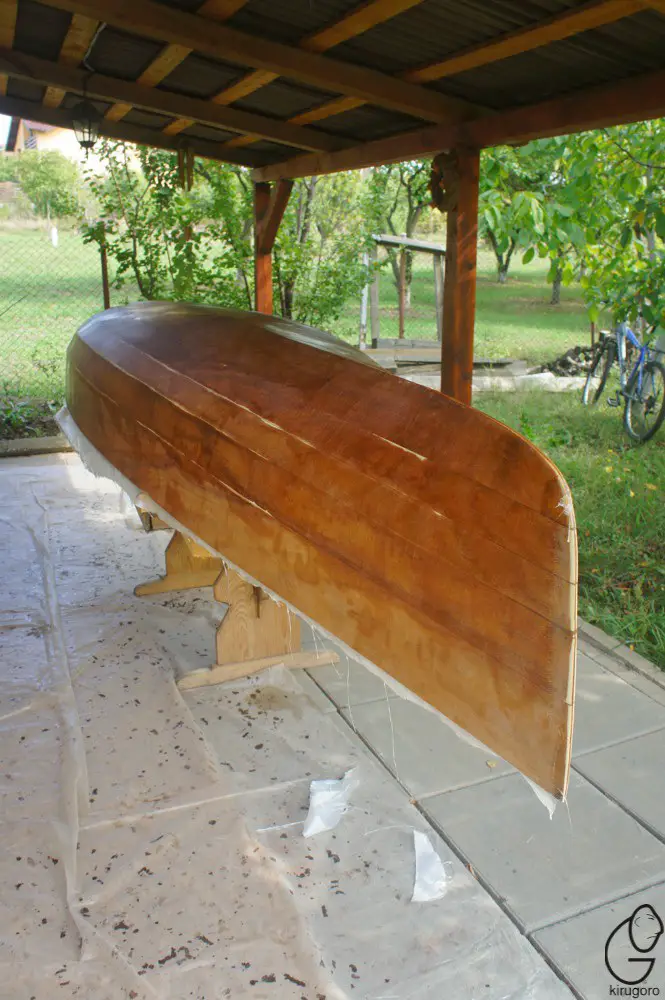
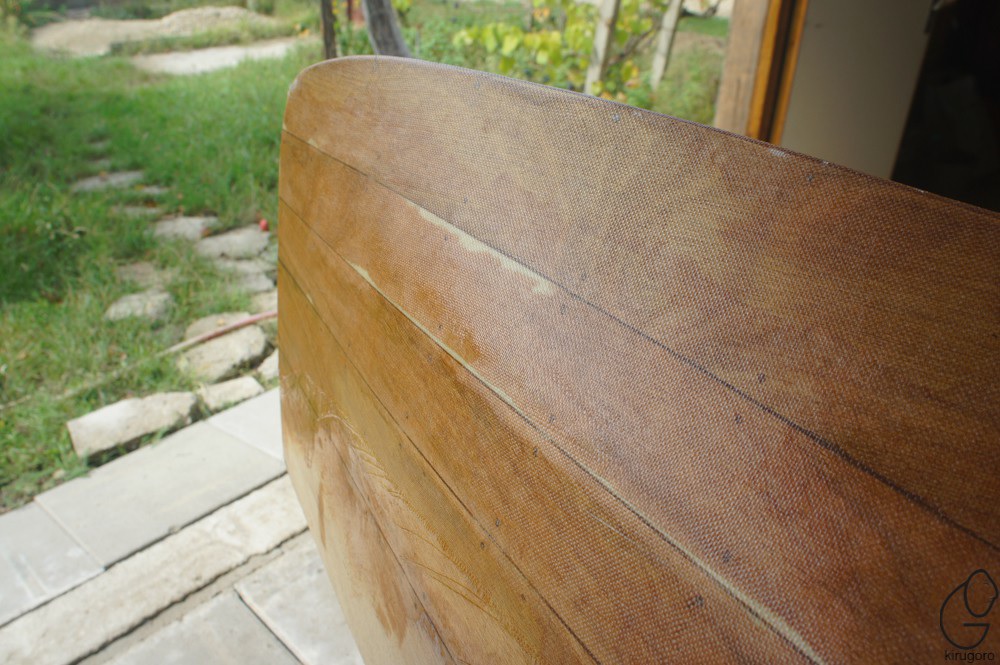
Once impregnated, the fiberglass fabric becomes perfectly transparent, so the boat will look like varnished wood, but if you want to color it, just mix paint pigment (powder) into the resin.
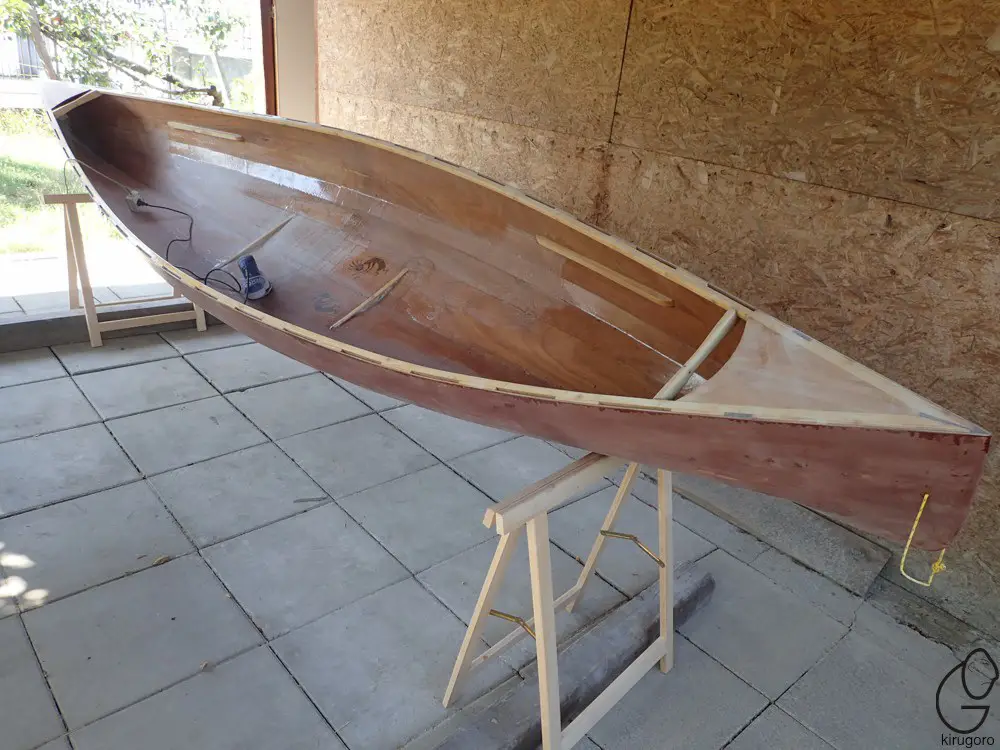
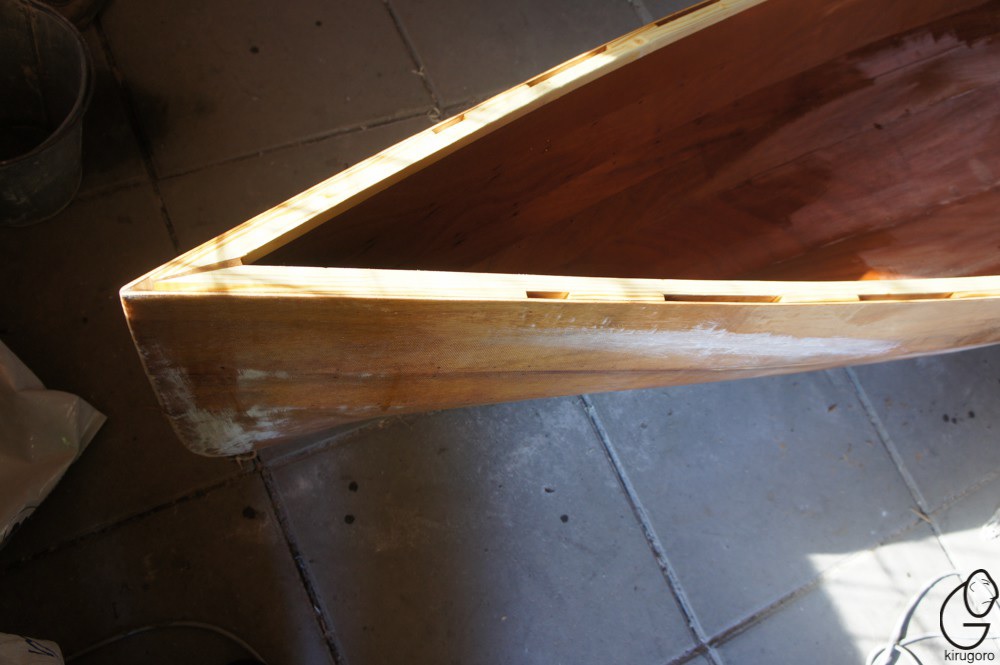
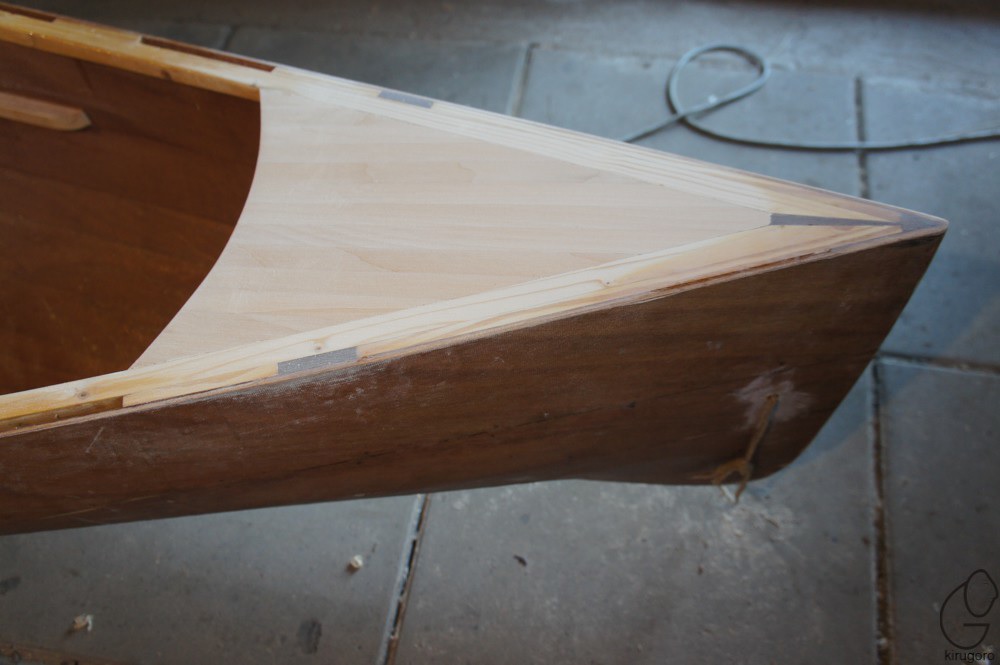
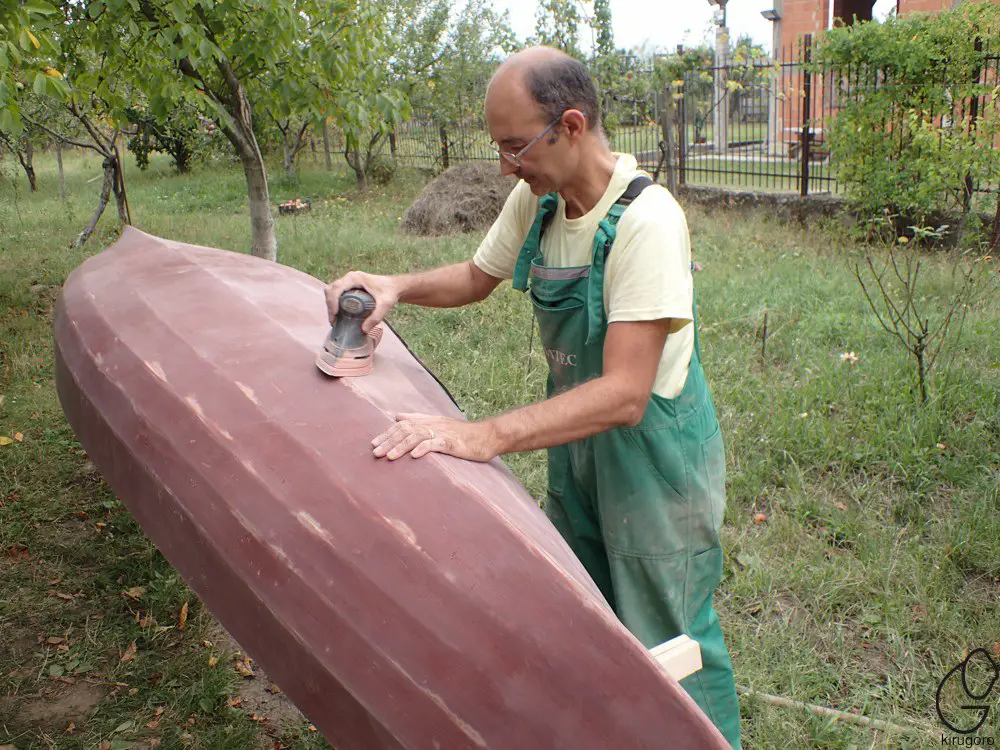
Two days after the last application, the resin is sufficiently polymerized to continue the work and we can proceed to strengthen the edges by gluing along them 25x25mm wooden slats called copings, and in the bow and stern we can make triangular decks of wooden slats or planks. After this, the hull of the boat only needs to be finished with increasingly finer-grained sandpaper and a final coat of UV-protected yacht varnish.
The canoe is finished and ready to be put on the water, but for a first paddle we still need seats for the paddlers and, of course, oars. Traditionally the seats are made as wooden frames inside which the seat is woven with a non-stretch synthetic thread. As fir or pine do not provide the necessary strength, hardwoods are used, preferably ash.
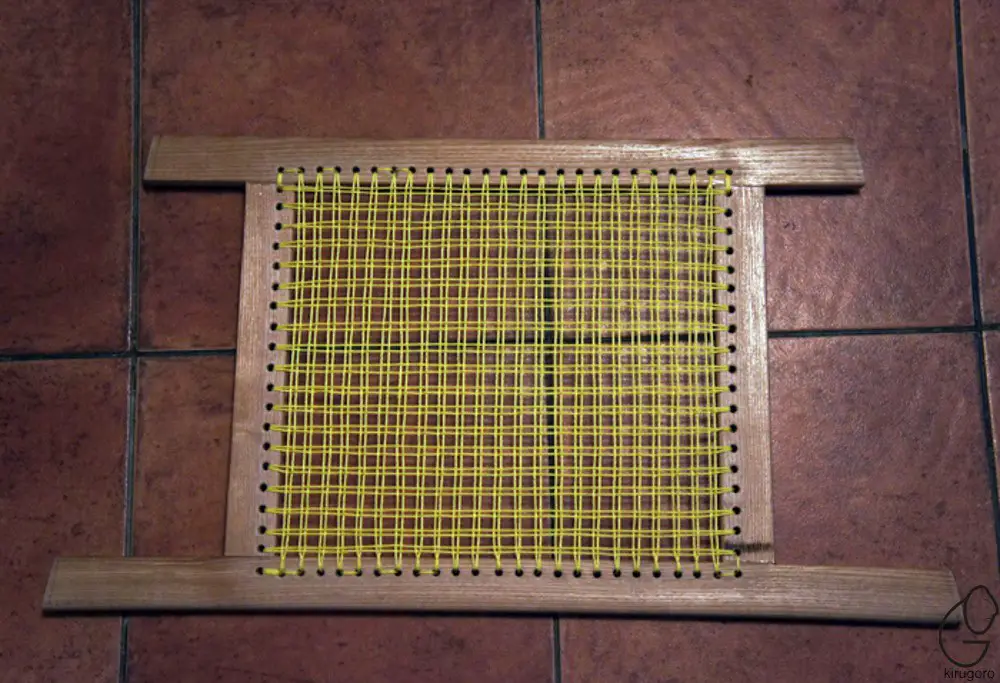
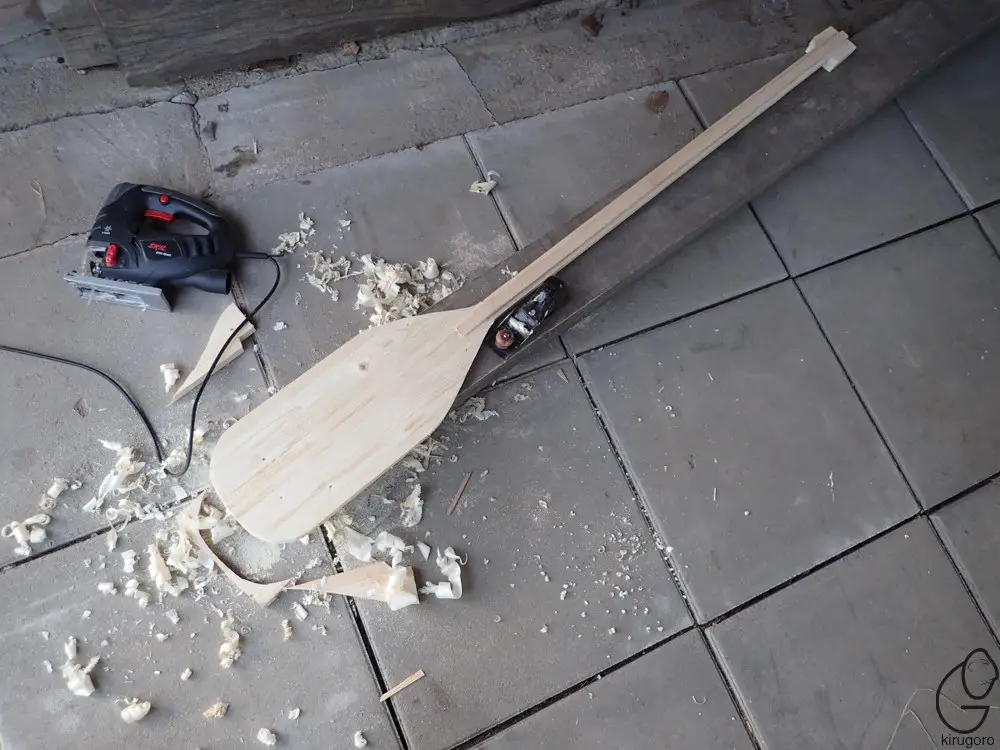
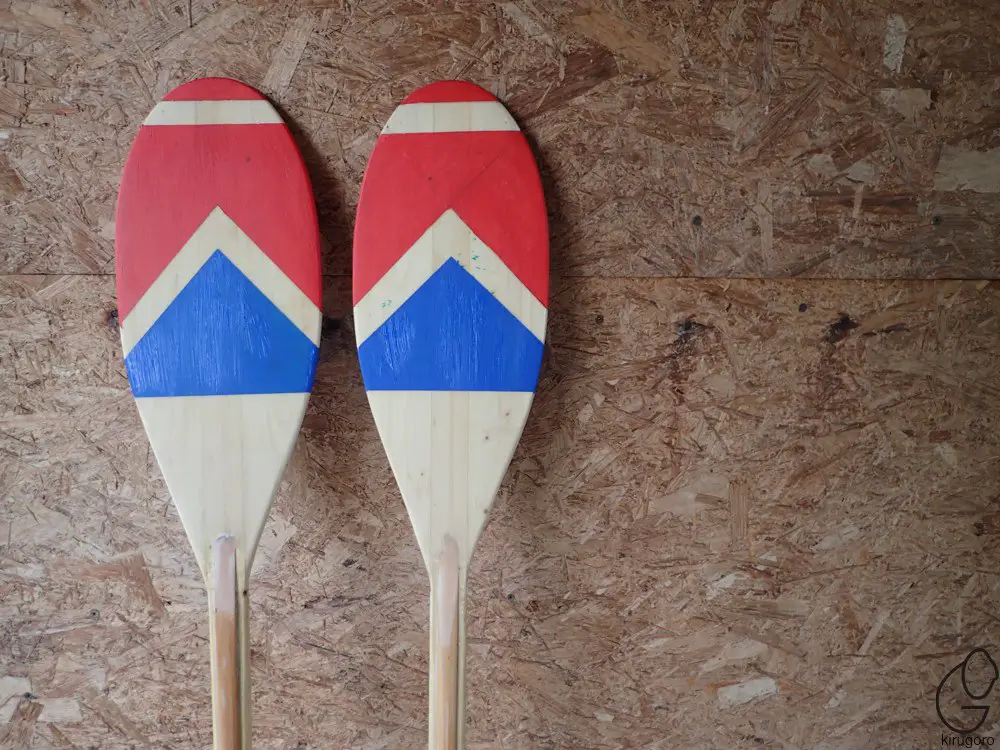
The paddles are made of pine slats glued together in the form of a panel and then sanded with sandpaper and sandpaperpaper. To protect the wood against water, the paddles are entirely laminated with fiberglass and covered with epoxy resin like the body of the canoe. If we are not in too much of a hurry to get out on the water, drawings can be made before the fiberglass is applied to the oars' feathers, which will be sent to the builder.
That's it. With that we are the proud owners of a pleasure boat that has given us satisfaction and a chance to boost our self-esteem. I said at the beginning of the article that a hand-made wooden boat is addictive: in most cases the first boat built is not the last. Most sailors stop when they run out of places to store their boats, but there have been plenty of cases where beautiful boats have been sold for nothing, just to free up space.
Add comment