I don't think there's anyone who hasn't seen chairs, armchairs, poles or other pieces of furniture that, although they have different shapes, have the design of wood continuous throughout. You've probably wondered if it's not just a design printed on paper, as it is laminate flooringwhich has no wood in it. But this time we're talking about wood. It's moulded plywood that can be used to make interesting furniture designs. Chairs made from moulded plywood are light and comfortable, resilient but very strong. The advent of moulded plywood was a turning point not just in the furniture industry. It is an interesting and attractive material, both for large furniture manufacturers and for passionate carpenters or designers.
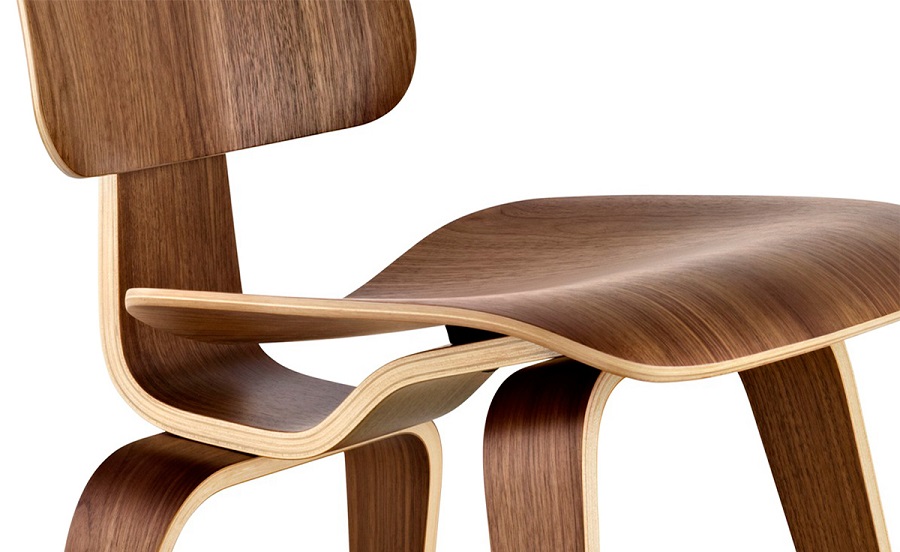
What is moulded plywood
I've talked about plywood before when I made a brief history or when we talked about wood-based panels. In short, plywood is a material that has been used for a long time in furniture making, and there are pieces of furniture in museums with plywood parts dating from the late 1700s to the early 1800s. Plywood is a derivative of wood that is made by overlapping and gluing veneers together. The resulting material is more stable and stronger, with a generous surface that can be worked like solid wood.
The furnaces can be laid perpendicular to each other or parallel along the fibre. In the first case the number of veneer sheets must be odd to balance the tensions. The resulting material is stiff, stable and light. In the second type the number of veneer sheets is important only in terms of the thickness of the resulting plywood. It is also called laminated plywood and is very elastic and strong. If, after applying the adhesive and overlapping the veneers along the fibre, drying is done in a mould under pressure, the result is moulded plywood.
Short history
The first attempts to obtain moulded plywood were made as early as 1830 by Michael Thonet. However, he has abandoned this direction, concentrating on bending solid wood. This is how he obtained - from curved beech elements - Thonet chairthe best-selling piece of furniture of all time.
In the 19th century there were various attempts - in Europe, the US and Canada - to obtain moulded plywood, but without impact on the industry. By the late 1920s designers and architects had discovered the versatility of plywood and were increasingly working with it. The important moment for moulded plywood's entry into industrial furniture manufacture was 1933. That's when mass production of the Paimio (more like an armchair), created in 1932 by the Finnish architect Alvar Aalto for the sanatorium in the town of Paimio. Soon the chair was exported to England, Germany and even the USA.
Another important moment for the evolution of moulded plywood was World War II. It was then that Mosquito plane with moulded plywood fuselage, the lightest and fastest fighter at the time and the one that flew at the highest altitude. During the war the aircraft was manufactured in England, Canada and Australia.
Other important moments in the history of moulded plywood furniture were the creation in 1952 of the Ant by Danish architect Arne Jacobsen and the collection of furniture pieces made in 1956 by the Ray and Charles Eames for American producer Herman Miller. These were the moments that set off a wave of moulded plywood furniture production around the world. Waiting rooms, canteens, restaurants, cinemas began to use them heavily and so moulded plywood furniture became commonplace. But that's not to say that there aren't still some spectacular and unique designer pieces out there.
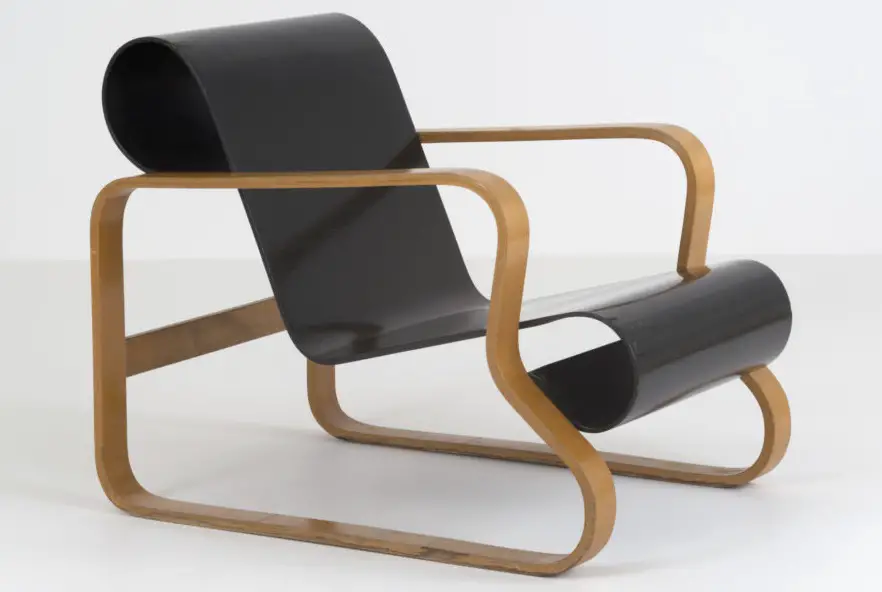
photo: alvaraalto.fi
What it takes to get a moulded plywood
Enough with the history, let's get back to the technique 🙂 To make molded plywood you need :
- veneer sheet
- adhesive
- mould, template
- press
Furnace used to obtain plywood is between 0.5 and 3-5 mm thick. Veneers below 1 mm are calledfAesthetic Urn and are used for plywood faces. They can be different in essence from each other so you can get plywood made of lime or plop with faces of nuc or cherry. The plywood will be easy and with very nice design. The thicker sheets are called technical furnishing.
Allocation adhesive must be correlated with the working technology. Certain types of adhesive are used for cold bonding (PVA), for hot processing, other types (ureoformaldehyde, resorcinic, phenolformaldehyde). Hot processors may also have emissions of free formaldehyde.
Matrix is the one that will give the final shape of the moulded plywood. Usually, when hot curing, the mould is part of the press. It's a mother-father type, meaning there is a form on which the veneer packet is placed and over which comes the "negative" of the original form which presses and heats at the same time. There is also the possibility of obtaining patterns in vacuum presses, in this case we still need a "negative" of the die. Regardless of how the mould is attached, 2D or 3D models can be obtained, depending on how elaborate the mould is.
Modelling can also be done with a template made of various materials, including moulded plywood. The veneers on which adhesive has been applied are shaped according to this template and clamped together with clamps to create the pressure needed for correct bonding. You have to work quickly to clamp them to the template before the adhesive starts to dry. It is good to check beforehand how the clamping will be done using the veneer pack without adhesive applied.
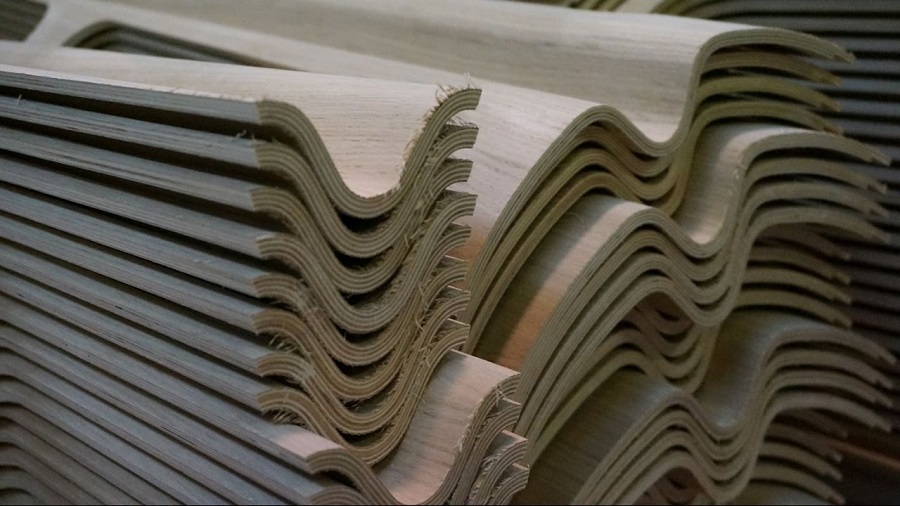
photo: youtube.com
Manufacturing techniques
How moulded plywood is made depends on whether the adhesive is cold or hot curing.
Obtaining through cold press is used to make one-offs or for designer or DIY projects. As mentioned above, templates cut from plywood or plastics are usually used. A flexible steel strip or sheet is placed between the template and the pack of veneer sheets to be pressed. During clamping, excess glue comes out and the plywood can stick to the template if there is no non-stick barrier. It's good to have excess adhesive applied to make sure the veneers stick to the entire surface. Many clamps should be used, clamped often, so that the pressure is as even as possible (this is why clamps are never enough 🙂).
The advantage of the method is greater flexibility. The disadvantage is the long pressing time, sometimes taking up to 24 hours for the plywood to take the desired shape.
Press hotcan be made in presses with normal heating or in CIF presses, i.e. using high frequency currents. The advantage of the second method is the very short working time, with 1.5-2 minutes needed for the plywood to emerge from the press ready to be shaped. Hot pressing is used mainly in industry where short curing time and identical pattern reproduction is needed.
CIF hardening is widely used worldwide and because the heat is evenly distributed within the adhesive layer. The resulting plywood is more homogeneous, with equal properties over the entire surface. High-frequency currents are supplied by a generator that is attached to the press. The generator can also work with 2 or more presses.
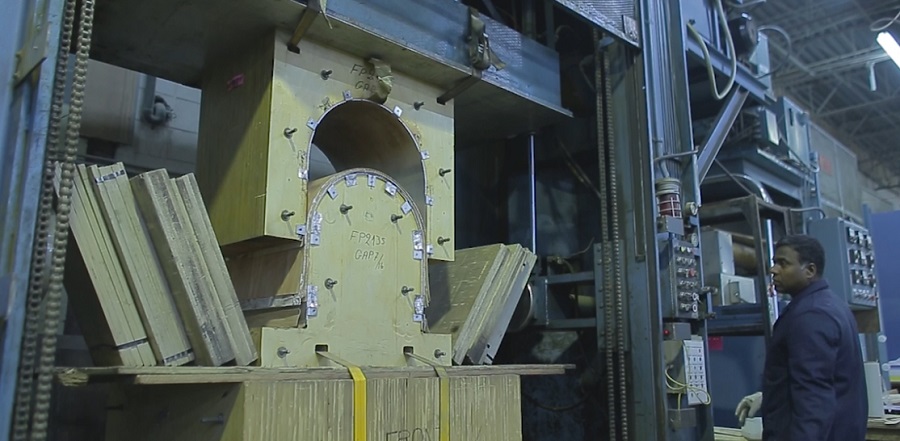
Properties, processing
After manufacture, moulded plywood can be processed like any other type of plywood or wood-based plywood. Immediately after pressing, the edges are cut to remove hardened glue leaks or loose parts. The result is clean edges on which the wood and adhesive layers are visible. Sometimes the differently coloured adhesive layer (shades of brown) gives a very pleasant and interesting appearance.
The moulded plywood can then be cut into narrower elements that will represent legs or arms of chairs and armchairs or can be machined on various traditional woodworking machines or on CNCs.
Fastening between moulded elements can be done with dowels, nails, screws or by gluing. Fastening to metal scaffolding can be done with screws. Despite its elasticity, plywood is a hard and strong material, and processing is easy.
The final quality of the plywood depends on the quality of the veneers used. Veneers without defects, fibre pull-outs or tears will result in very good quality plywood. After processing and jointing, the moulded plywood object can be sanded and finished in the same way as veneered furniture.
I hope you find the information interesting. If you think it would be useful to others, you can share it. If you have any additions, questions or comments, please leave them below in the space provided.
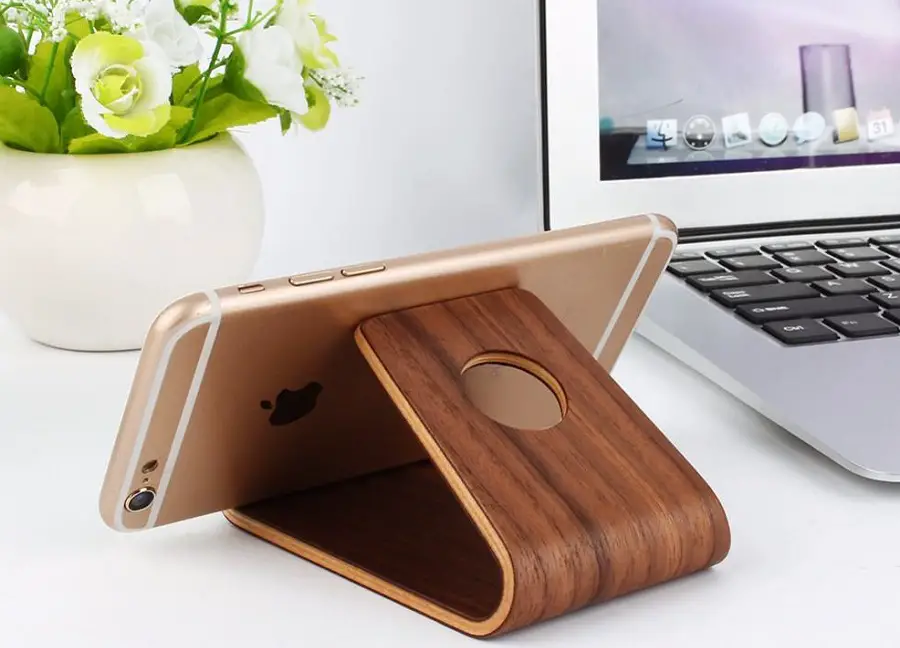
Hello
Thanks for a very good, informed and useful article.
Plywood is regaining its place and appreciation in the furniture manufacturing industry in Romania and beyond.
I am very interested in details of the adhesives used in the industry by the manufacturers of wood boards.
Thanks in advance if you could recommend some sources of information on this subject.
Good luck for the future!
Hello.
Thanks for your appreciation.
Indeed, plywood is no longer just that material used as a backing for furniture.
Unfortunately, in the field of adhesives, there is little information on Romanian websites. We have written a bit about adhesives, but more about the "aracet" type or for DIY activities. About the industrial ones we touched lightly on the subject in the article about formaldehyde amine. I intend to write an article on industrial adhesives soon.
All the best!
This information is very important,
Many thanks to the promoters