The most commonly used method of application of stains, varnishes and paints is spraying. Whether in workshops or factories with finishing lines In order to reach the wood and form the film, the material passes through one or more spray guns. Unfortunately, there is no gun, no matter how good, that can transfer the lacquer to the piece at 100%. Thus a very small amount of lacquer droplets remain in the air in the room where the spraying takes place. In the case of spray lines the problem is solved because spraying takes place in closed areas connected to the exhaust system. However, when spraying takes place in a workshop or factory, spray booths must be installed in order to avoid problems with film quality or high levels of noxious emissions.
What over-spray is, the factors that influence it and how the lacquer film and the air in the working environment are affected
By spraying the lacquer is transformed into very fine particles. Some of these particles end up on the object to be varnished and form the film. But another part remains in the air and is lost. In the industry this amount of lacquer is called over-spray.
Over-spray depends on several factors:
- type of gun,
- his performance,
- method of application (conventional, airless, airmix, electrostatic)
- the shape of the object being finished,
- air pressure.
The lost quantity ends up in the working environment making the air difficult to breathe and can even affect health if the operator stays for a long period in such an environment. In addition, if the sprayed material is flammable, a high concentration of vapour increases the risk of fire.
Film quality also suffers because the varnish particles dry in the air and fall onto the piece before the deposited varnish film has dried. This varnish powder is embedded in the film and becomes rough. In the industry the term "gassing" of lake film.
These inconveniences are solved if the spraying area is equipped with spray booths.
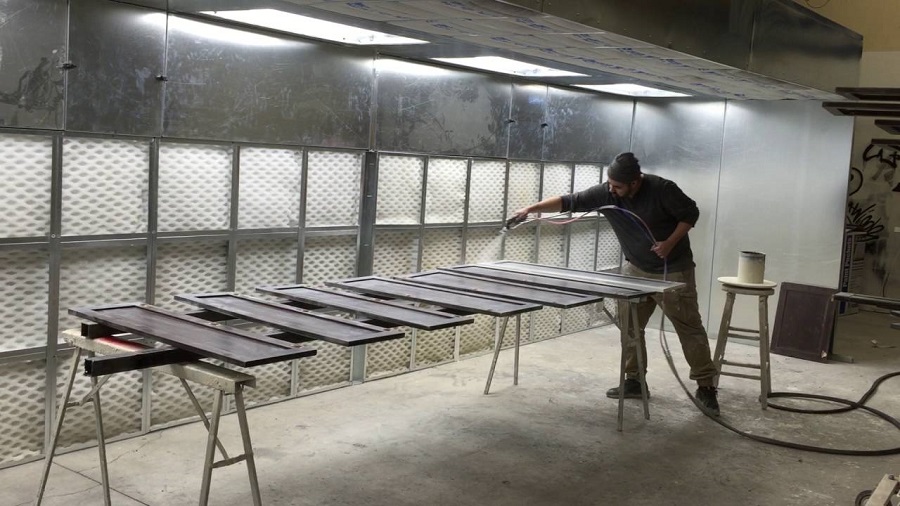
What is a spray booth
The spray booth is a facility that removes stale air from the premises and purifies it by passing it through filters. Basically the air is sucked in by a fan and taken out, but not before the varnish particles are removed by filters.
Filters that retain fine lacquer dust can be dry or wet. A dry filter consists of a cluster of fibres through which air is forced to pass. The dry lake will be retained by these fibres to a fairly large extent, making the air cleaner. Before being released into the atmosphere, the air can pass through several such filters, with the percentage of retention increasing.
High-performance filters have several layers. The air passes through a first layer of cardboard, which traps large particles of varnish, then through a layer of polyester, fibreglass or other effective filtering material that will trap the very fine particles.
Wet filter is a curtain of water. The stale air is absorbed through the water curtain, with the varnish particles remaining in the water. Substances (coagulants) are then put into the water to precipitate the varnish and collect the particles so that it can be purified and filtered.
There are simple and less efficient booths, but also booths equipped with high-performance filters that also retain volatile organic compounds (VOCs), with heating/cooling systems for the air brought into the spray chamber or that have areas set up for drying painted parts. Let's take a look at some of them.
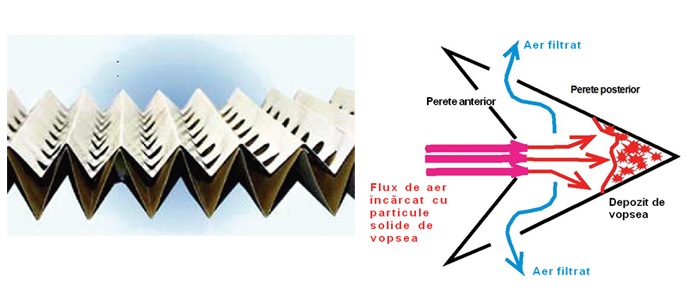
Types of spray booths
1. Absorbent walls
Using absorbent wallsare the easiest way to remove varnish particles from the spray area. They are not effective if they are placed in the space where mechanical work is being done and there is a lot of wood dust. In order to obtain quality films the spraying must be done in a separate, enclosed space. A booth can only work in an open space if there is a very efficient dust suction nozzle at each mechanical processing location.
The absorbent wall is the easiest way to eliminate spray losses. Simple installations involve a metal construction, filters and a fan that absorbs the air, passes it through the filters and releases it into the atmosphere.
They can be of different sizes and have one, two or more spraying places. The power and number of fans vary according to the size of the booth. A booth is efficient if it manages to change the entire amount of air in the room several times in an hour. For example, an efficient one-spray booth, measuring 2 m long and 2.20 m high, should have a fan with a flow rate of around 7000 mc/h.
Depending on the type of filter used, the absorbent walls can be dry-filtered or water-filtered. Absorbent wall with dry filter is a very adaptable version and can be installed in any space. The air-suction fan is mounted on the roof, behind or to the side of the cab. In front of the absorbent wall is the place where the spraying is done.
The purified air is collected with a tube and either discharged outside or taken to other more efficient filters that can retain volatile organic compounds (carbon filters).
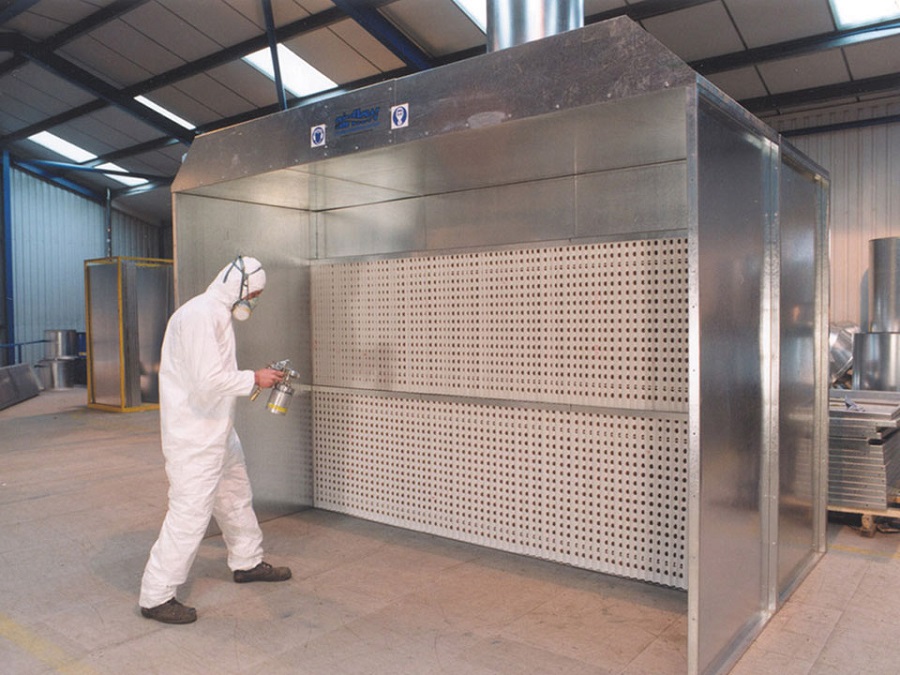
Absorbent walls with water filterhave a curtain of water running down a tin wall. In the past, all cabins in factories had a water filter. To be able to fit them, there had to be an industrial water supply. Now there are cabins with a water recirculation system. The spray booth is fitted, supplied with water which is recirculated for a period, then changed. The water contains coagulants that make the residues left after filtration settle and can thus be easily removed.
The air is sucked in by the fan and passed through the water curtain. Filtration is all the more effective as the air is passed through the water several times before being released into the atmosphere. From a design point of view, there are solutions for directing the air along a particular path or placing successive waterfalls in the path of the sucked air. In this case too, if advanced filtration is required, the air is directed to special filters that retain hazardous substances.
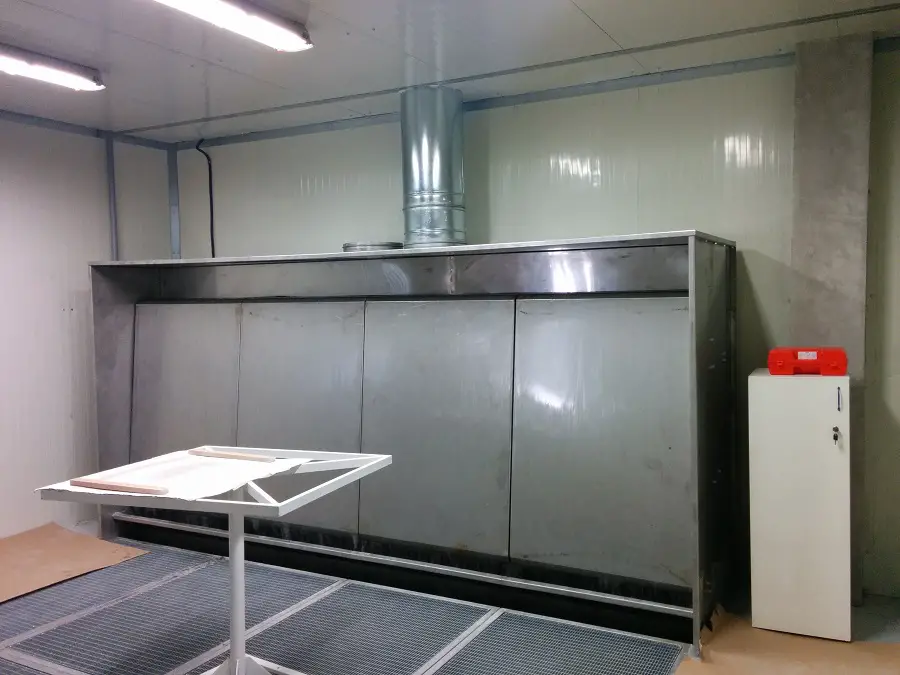
2. Spray booths for laboratories or workshops with small volumes of lacquered parts
They are cabins that follow the principle of dry filter cabins, but are small in size. They can be fitted with wheels for easy moving. The volume of air sucked in is small and the air is drawn in from the inside, not from outside.
They are very adaptable cabins with different shapes and sizes. They can be used in laboratories to test a varnish, being basically a box into which the hand with the gun and the object to be finished fit. They can be adapted for workshops and small factories so that they take up as little space as possible.
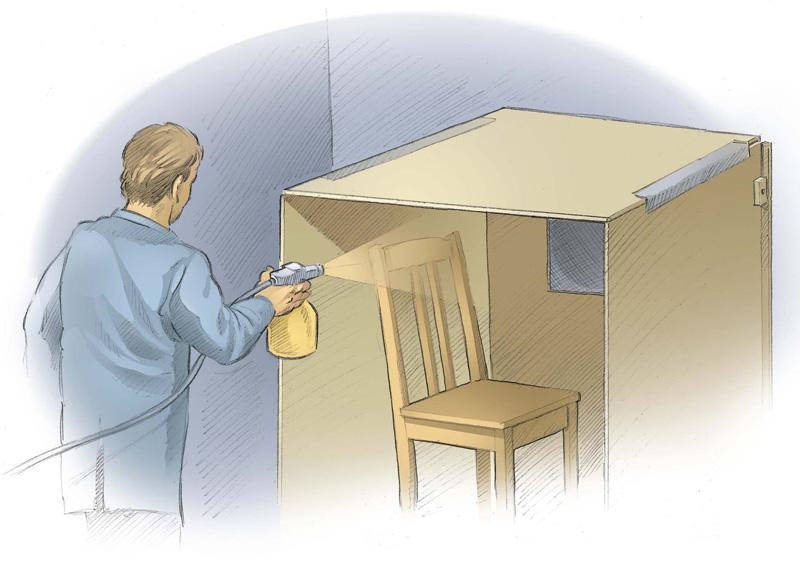
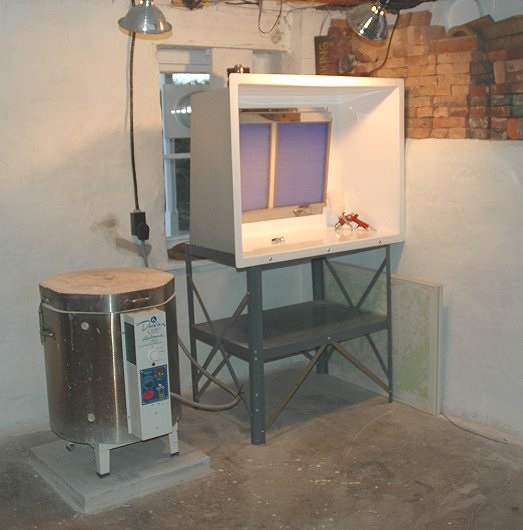
3. Pressurised spray booths
These are booths without which it is very difficult to achieve quality gloss finishes. We used to say that the enemy of spray quality is dust. If you look achieving a high gloss there must be no dust in the spray area, and an ordinary spray booth cannot ensure this. No matter how isolated it is from the processing areas, there will always be a source of dust. On the glossy film, the small particle of dust will be greatly exaggerated in size and effect.
The problem is solved using pressurised spray booths. It is a closed enclosure in which a slight overpressure is created by introducing more air than is taken out. This prevents dust from being drawn in from the outside. In order for the overpressure to persist over time the cabin must be very well sealed.
It is good to know that immediately after installation the air must be recirculated for a while to get rid of dust inside the cabin. Filters and insulation used inside are sources of dust and should be thoroughly shaken out and vacuumed before work actually starts.
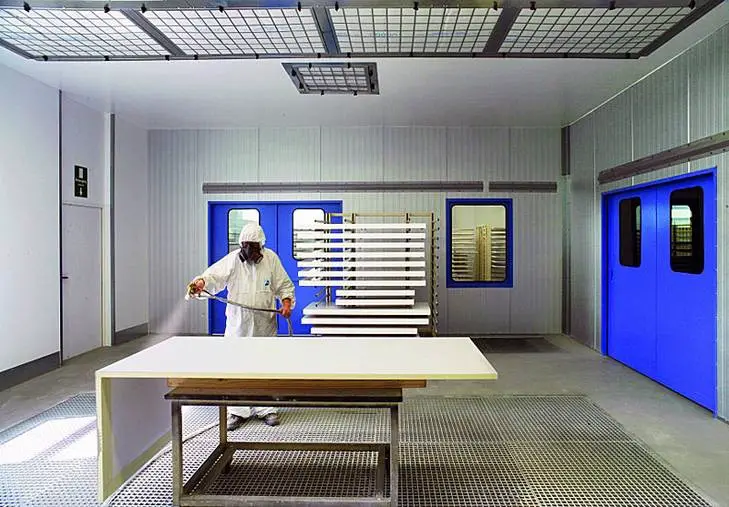
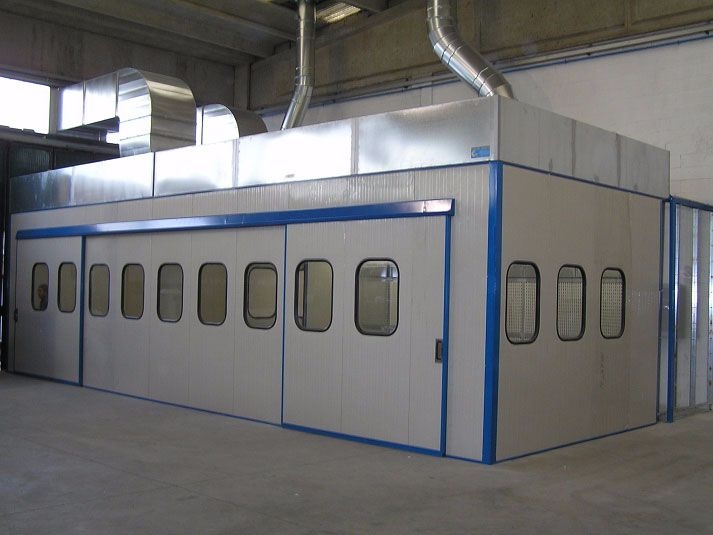
Guns with very good material transfer efficiency per piece
Spray losses of varnish translate into actual losses of money. That's why some are turning to other systems and ways of varnishing. In order not to lose their customers, spray gun manufacturers are continually improving their technologies to minimise losses.
This is also the case of Sames Kremlinwhose distributor in Romania is Falk Consulting. Sames Kremlin produces guns with material transfer rates up to 80-90% and even higher. About Xcite pistol, which has a transfer efficiency of up to 86% I already told you. SFLOW™ 275 & 450 is another efficient spray gun with a transfer rate of 81% and airless application. It is lightweight and very easy to handle.
But Nanogun AIRMIX®with a transfer efficiency of 93%, exceeds all expectations. It is applied electrostatically and is very suitable for spraying medium viscosity paints. The compressed air overflow allows the jet to reach the most hidden places and is very suitable for lacquering objects of various shapes.
A booth is mandatory if you manufacture items that you spray-finish. You won't be able to get a quality film if you apply varnish in an open space where varnish particles and dust float freely. But remember that a spray booth won't work wonders, and you'll need a quality spray gun to reduce spray spillage.
Add comment